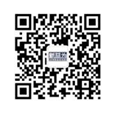
微信公眾號二維碼
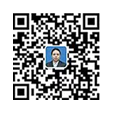
微信咨詢顧問二維碼
影響車間效率的幾大殺手?新益為效率提升咨詢公司概述:
一、不會高效利用工作時間
目前,許多服裝廠大包生產的有效運行時間 (平車高速運行時間) 與輔助運行時間相比,時間剩余率高,設備利用率低。有些公司都是傳統的大包生產模式,有效運行時間極低,輔助運行時間極高。
精益生產咨詢
為什么會有這么長的輔助時間?因為傳統的大包流水生產模式,給生產前期部門造成很多寬松的時間,會給前期面輔料部門的配送,提供隔三差五的缺這缺那的空隙,只能挑先做的工序做,從裁片裁剪好了以后到成為成品,各個工序之間需要不停地人工搬運傳遞、計數、捆扎、來回換工序等,這樣可能導致衣片錯號,產生大量誤工和混亂,最終導致設備利用率低,效率遲遲難以提升。
二、工序之間協調不流暢
在生產流水中,絕大多數工廠在班組常出現“忙的忙死,閑的閑死”的現象,這在一線生產中是最常見,也是最影響生產效率的。這種問題與車間生產管理排單、班組長的工作安排有很大的關系。
在服裝流水線生產過程中,工序與工序之間不能平衡,是制約提高生產效率的最大“瓶頸”,往往這些“瓶頸”多數集中在復雜工序上。而此時,效率的高低完全取決于一個班組長的管理調度能力的好與差,一個好的班組長,能夠及時地分析判斷“瓶頸”工序在哪里,能夠及時調整調度,從而提高效率。
三、個人操作方法不規范
產生不良品返工導致效率低,絕大多數服裝工廠的縫制車間,因為款式與貨期的狀況,一個班組要同時上2–3個款,在這個時候,很多生產管理人員對員工要重復指教的可能性不大,員工生產技巧掌握度就大大降低,員工對自己的生產質量要求不是十分明確,生產管理不能及時糾正,又是大包流水生產,一旦發現質量問題就會造成大量返修,一到出貨時間就忙、亂、差、錯。
而在縫制環節,新產品剛開始上線,或者某一款產品急于下線,往往前者的特征是負責前面幾道工序的員工來不及做,負責后面工序的員工卻沒活可做;后者的特征恰恰相反,負責前面幾道工序的員工沒活可做,而負責最后幾道工序的員工卻又忙不過來,這些都是效益低下的原因。
四、品質大量返修的問題
傳統服裝生產流水線經常出現品質問題,品質事故出現之后,就會造成很多工序跟著返修,找不到責任工序,員工之間矛盾與互相扯皮,已有的品質處罰規定無法落實,而責任人得不到處理以后,下次依然如故,并且還有更多的人效仿,最終影響貨期與質量,使原本能產生效益的生產數量在處罰上降低效益。
五、不會破解“勞工荒”
要達到精益生產,建議企業需要5個實施手法:
1、做精益生產,首先是目標明確
對公司而言,就是為了生存,或者生存得更好。對員工來說,就是要用更少的時間賺到更多的錢,能夠有更多的休息時間。而對于管理人員來說,學會一門更為先進的管理技術和方法才是最為重要。
2、JIT和自動停線,精益生產的兩大支柱
精益生產要求各部門以生產為中心,按計劃要求跟進落實,做好“服務員“的本職工作,但事有意外,在問題發生時必須先停下來,找到問題、解決問題!
3 、精益最高境界是每天按計劃完成目標產量
達致這個目標最最重要的前提就是平衡化生產,人的能力有大小、工序有難易,必須合理分配工序,及時做好平衡,做到人盡其才人盡其能。
4、GSD/GST標準工時是平衡化生產的基礎工具
有了標準工時才能了解員工的技能程度,才能確定每個工序的真實時間。如果暫時沒有配置GSD標準工時軟件系統,也應該由IE人員進行秒表測時和攝像測時。
5、消除浪費,是精益生產的根本動力
最簡單有效的精益生產,如果暫時不能做到真正的單件流水,不妨考慮下面幾招:嚴控半成品,半成品越少越好!優化流水,減少搬運!及時發現、及時解決。
影響車間效率的幾大殺手?以上就是新益為效率提升咨詢公司的相關介紹,做好企業的效率提升工作就是為精益生產管理活動打下基礎,讓精益生產管理在企業中發展有一個良好的前提。
建立生產有序、管理順暢,操作規范,士氣高昂、高質量、低成本、短交期的作業現場;
為企業規劃設計一套由內到外的形象升級,外觀視覺價值體現、內在的管理內涵體現;
全員參與設備管理高產出和低成本運營,提升設備管理能力,維護能力,提高效率
構建班組生產管理體系、循環評價、人才育成、持續改善、績效管理、文化養成體系;
提高產品質量、降低生產成本、縮短交期、增加利潤,讓管理更系統科學,執行力更強
對工廠的各個組成部分進行合理安排,以提高生產效率、降低成本、優化物流、改善工作環境等