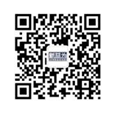
微信公眾號二維碼
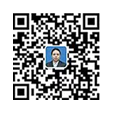
微信咨詢顧問二維碼
新益為精益生產咨詢公司概述:事實上,真正成功實行精益生產方式的企業并不多。有的公司在實施一段時間后,確實也改善了產品質量,生產周期也明顯縮短了,但不久后又逐漸回復到原來的景象。要讓精益生產方式持久地在企業生根,除了學習他們的制度與原則外,還需要充分了解精益生產的理論架構。
精益生產理論架構
數十年來,精益生產方式透過不同學者的觀察、調研,與豐田內部人員的發表、傳授,已經形成一個完整的管理體系。美國密西根大學教授Jeffrey Liker通過對美國豐田汽車公司的長期觀察及調研,歸納出上圖的精益生產的理論架構,對于企業學習精益生產方式提出了更具體的原則與方向。下面對這一理論架構作出解釋。
一、長期的理念
精益生產企業非常重視長期的思維,從顧客及創造社會價值出發,不會為了短期利益而改變長遠的戰略思維。基于此一理念,管理決策也是以長期理念為基礎的,即使為了維護長期理念而造成短期的財務成果受到影響,也不會改變既定的決策。這與一般追求短期財務成果的經營理念有極大的不同。當領導高層面對抉擇時,仍堅持既定的長期理念是極為困難的,這也是許多企業無法持續維持精益生產方式的根本問題。美國的安然公司就是一個鮮明的案例。上世紀80年代安然的主營業務是休斯頓的天然氣及電力交易合約,腳踏實地,穩扎穩打,業績雖不轟轟烈烈,卻也是呈緩慢成長,但后來由于高階領導層只注重短期財務利益,不但公司破產倒閉,導致數萬名員工幾乎是家財散盡,也造成巨大的社會成本。而反觀豐田汽車公司的理念,他們認為賺錢的目的不是為了公司的利益,也不是為了公司的股票上漲。賺錢的目的是為了能夠持續進行投資、繼續營運,為了安定社會、造福員工。例如,在1990 年,他們為了重環保、保護自然資源,開始發展21世紀的新型汽車,終于在1997 年研發成功了油電混合動力車。在能源價格高漲的今日,更可印證這種長期理念的重要。
二、建立正確的流程以產生優異的成果
精益生產方式是一種流程導向的思維,認為有正確的流程才能產生期望的結果,精益生產企業對此深信并且奉行。流程建立在低成本、高柔性、高質量與高安全性的目標基礎上,并且從經驗中不斷地改善,讓流程更卓越。許多企業學習精益生產方式最容易看到,最先開始學習的也是流程,但這只是皮毛而已,多數的企業都只是學到流程的表象,這是導致精益生產失敗的主因。精益生產方式是建立許多合乎最終經營理念的正確流程,并且透過許多工具監督這些流程徹底被執行,若執行過程有異?;蚱x常軌時,可以立即被發現與改正。這些流程與工具為:后拉式生產、節拍(TAKT)與平穩化生產、安藤燈、看板等。
精益生產方式以建立無間斷作業流程讓生產過程的問題浮現,透過后拉式生產制度來避免生產過剩,以平穩化的計劃與排程讓各工序工作負荷穩定,使用安藤燈來執行與建立遇到問題立即暫停以解決問題的機制、在源頭就重視質量的文化(自動化),以職務標準書作為授權員工與持續改善的基礎,以看板作業溝通前后工序的進度、是否遵行計劃作業的檢核工具,車間中處處可見視覺化的看板,讓作業中的問題無所遁形。經由建立正確的流程、有紀律的執行流程;然后再持續改善流程,產生更好更正確的流程,從而使得精益生產企業的經營成果優于一般企業用。
三、發展員工與事業伙伴為組織創造價值
精益生產企業始終將員工視為企業最重要的資產,不論是在企業營運高峰還是低谷,都不會改變。就算是在業務量萎縮時,也不會輕易解雇員工,而是將多余的人力投入改善活動中,期望在運營回復到正常水平時,經驗豐富的員工可以立即上場。他們從開始就下功夫,招募與培訓了解且認同企業理念的人員,并且栽培這些人成為各階層的領導者,再由這些領導者教導其它員工,逐漸地讓整個企業的人員思想一致,認同企業理念與目標。如此,在執行各部門工作時,可以落實執行紀律,即便為了落實流程作業而使得工作。上較為麻煩,也不愿違背作業標準書的要求。在豐田汽車被徹底執行的一項制度是“安藤燈”,這是由自動化理念所產生的制度,它是用來促成員工持續改善與持續發展的工具。當流水線出現問題而員工無法自行排除時,員工就自然地啟動安藤燈請求支持,領班立即協助探討與解決問題,在此過程員工不因顯示問題而被處罰,更因此被鼓勵。久而久之,企業內所有員工都具有改善的意識,也成為解決問題的高手,整個組織的競爭力必然優于其它企業。
除了員工外,精益生產企業將供貨商也視為事業伙伴,當成企業的重要資產看待。從尋找好的合作伙伴開始,就以長期互利、互惠的方式隨時協助事業伙伴以共同成長,提升改善的意識與改善的能力。對供貨商來說,因為精益生產的平穩化,供貨商的需求也更均衡平穩。雖然,供貨商與精益生產企業往來,背負著持續改善的壓力,但在長期的栽培與學習下,這些供貨商更樂于與精益生產企業成為生命共同體,如此,創造了整個供應鏈的價值。
四、持續解決根本問題成為學習型組織
精益生產的最高境界是學習型組織,整個組織上上下下,持續學習、辨識問題的根源、、深入分析、省思,以預防問題的再發生。精益生產方式要求員工凡事都要親自到現場了解問題的真相,了解發生什么問題?問題的原因何在?并以親自證實的人、事、物等資料做思考與判斷。持續解決根本問題的重點與工具為:現地現物、大野園圈與五個為什么。
現地現物:現地現物的字面意思是親自到實際的地點察看實際情況,掌握一手信息,以深入理解問題的狀況,不是拿著屬下的呈報數據做分析或直接往上呈報。
大野圓圈:是由有豐田生產方式之父尊稱的大野耐一發明的。大野耐一在車間的地板畫一個圓圈,要求新進的工程師站在里面一整天,觀看車間的作業流程與自行思考看到的問題。目的是要培訓員工去質疑所看到的作業,分析為什么這么做與評估如何改善。這個故事流傳下來,也成為精益生產企業很重要的改善精神。
五個為什么:大野耐一為了找出隱藏于問題源頭背后的根本原因,經常在車間對一個問題,連續問五次為什么,來探究事件的根本原因。這種連問“五次為什么”的過程會層層向上溯源,也成為精益生產方式的重要原則。
要持續解決根本問題,最重要的是先有正確的流程,通過探究過程出現的問題加以改善,再將改善后的做法修正流程,成為較佳實務,再以較佳實務進行作業,若再出現問題,再進行改善,如此讓持續改善成為一種習慣。
建立生產有序、管理順暢,操作規范,士氣高昂、高質量、低成本、短交期的作業現場;
為企業規劃設計一套由內到外的形象升級,外觀視覺價值體現、內在的管理內涵體現;
全員參與設備管理高產出和低成本運營,提升設備管理能力,維護能力,提高效率
構建班組生產管理體系、循環評價、人才育成、持續改善、績效管理、文化養成體系;
提高產品質量、降低生產成本、縮短交期、增加利潤,讓管理更系統科學,執行力更強
對工廠的各個組成部分進行合理安排,以提高生產效率、降低成本、優化物流、改善工作環境等