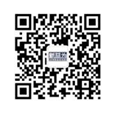
微信公眾號二維碼
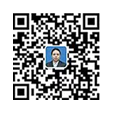
微信咨詢顧問二維碼
企業要進步,管理就不能停留在以前的模式上,就需要向精益管理過渡。很多管理者都想成功推行精益管理,但不知道該如何入手,處在迷茫的階段。下面新益為精益管理咨詢公司就具體說說精益管理成功的秘訣。
精益管理
一、建立看板體系
就是重新改造流程,改變傳統由前端經營者主導生產數量,重視后端顧客需求,后面的工程人通過看板告訴前一項工程人員需求,比方零件需要多少,何時補貨,亦即是“逆向”去控制生產數量的供應鏈模式,這種精益管理方式不僅能節省庫存成本(達到零庫存),更重要是將流程效率化。
二、強調實時存貨
依據顧客需求,生產必要的東西,而在必要的時候,生產必要的量,這種豐田獨創的生產管理概念,在80年代即帶給美國企業變革的思維,現已經有很多企業沿用并有成功的案例。
三、標準作業徹底化
他們對生產每個活動、內容、順序時間控制和結果等所有工作細節都制定了嚴格的規范,例如裝個輪胎、引擎需要幾分幾秒鐘。但這并不是說標準是一成不變的,只要工作人員發現更好更有效率的方法,就可以變更標準作業,目的在于促進生產效率。
四、排除浪費、不平及模糊等
排除浪費任何一絲材料、人力、時間、能量、空間、程序運搬或其他資源。即排除生產現場的各種不正常與不必要的工作或動作時間人力的浪費。這是精益管理方式最基本的概念。
五、反復問五次為什么
要求每個員工在每一項任何的作業環節里,都要重復的問為什么(Why),然后想如何做(How),以嚴謹的態度打造完美的制造任務。
六、生產平衡化
精益管理中的平衡化指的是“取量均值性”,假如后工程生產作業取量變化大,則前作業工程必須準備最高量因而產生高庫存的浪費。所以豐田要求各生產工程取量盡可能達平均值,也就是前后一致,為的是將需求與供應達成平衡,降低庫存與生產浪費。
七、充分運用“活人和活空間”
在不斷的改善流程下,豐田發現生產量不變,生產空間卻可精簡許多,而這些剩余的空間,反而可以做靈活的運用;相同人員也是一樣,例如一個生產線原來六個人在組裝抽掉一個人,則那個人的工作空間自動縮小,空間空出來而工作由六個人變成五個人,原來那個人的工作被其他五人取代。這樣靈活的工作體系,細稱呼為“活人活空間”即鼓勵員工都成為“多能工”以創造最高價值。
八、養成自働化習慣
精益管理的自働化不僅是指機器系統的高品質,還包括人的自動化,也就是養成好的工作習慣,不斷學習創新,這是企業的責任。這點完全如松下幸之助本的概念。東西和做人一樣,通過生產現場教育訓練的不斷改進與激勵,成立學院讓人員的素質越來越高,反應越快越精確。
建立生產有序、管理順暢,操作規范,士氣高昂、高質量、低成本、短交期的作業現場;
為企業規劃設計一套由內到外的形象升級,外觀視覺價值體現、內在的管理內涵體現;
全員參與設備管理高產出和低成本運營,提升設備管理能力,維護能力,提高效率
構建班組生產管理體系、循環評價、人才育成、持續改善、績效管理、文化養成體系;
提高產品質量、降低生產成本、縮短交期、增加利潤,讓管理更系統科學,執行力更強
對工廠的各個組成部分進行合理安排,以提高生產效率、降低成本、優化物流、改善工作環境等